Why does laser welding create stronger joints compared to traditional welding methods?
Laser welding is a high-precision welding technique that uses a focused laser beam to join metals and other materials.
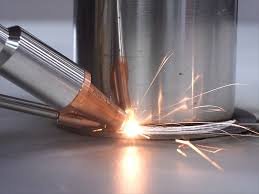
Laser welding is a high-precision welding technique that uses a focused laser beam to join metals and other materials. Unlike traditional welding methods, which rely on arc, resistance, or friction, laser welding provides a concentrated heat source, allowing for deep penetration and minimal distortion.
How Laser Welding Works
The process of laser welding involves directing a laser beam onto the material's surface. The intense energy melts the metal, forming a molten pool that solidifies into a strong joint. Depending on the material type and thickness, different laser types—such as fiber, CO₂, or Nd:YAG—are used to achieve optimal results.
The strength of a weld depends on several factors, including:
- Heat input and control
- Penetration depth
- Solidification behavior
- Metallurgical properties
Laser welding provides a unique combination of these factors, leading to improved joint integrity and durability.
Precision and Heat Control in Laser Welding
One of the primary reasons why laser welding creates stronger joints is the precise control over heat input. Traditional welding techniques often introduce excessive heat, leading to thermal distortion, residual stress, and material weakening. In contrast, laser welding delivers a concentrated heat source, minimizing the heat-affected zone (HAZ).
A smaller HAZ means less microstructural alteration, which helps maintain the material's original strength. By reducing grain growth and phase transformations, laser welding ensures that the joint remains structurally sound.
Deep Penetration and Narrow Welds
Another advantage of laser welding is its ability to create deep, narrow welds. This deep penetration is achieved through a phenomenon known as keyhole welding, where the laser creates a vaporized cavity within the material. The keyhole effect allows for stronger fusion between the metal parts, enhancing the overall mechanical properties of the joint.
In traditional welding methods, shallow penetration often leads to weak bonds, requiring additional filler materials. Laser welding eliminates the need for excessive filler, ensuring a purer weld structure.
Microstructure and Metallurgical Properties
The metallurgical properties of a weld significantly influence its strength. Laser welding produces refined grain structures, which contribute to enhanced mechanical performance. The rapid solidification process limits grain coarsening, reducing the likelihood of cracks and defects.
Additionally, laser welding minimizes oxidation and contamination, preserving the material's integrity. The cleaner environment results in a high-quality weld with better fatigue resistance.
Comparing Laser Welding to Traditional Welding Methods
To understand why laser welding creates stronger joints, it is essential to compare it with other welding techniques:
- Arc Welding: Uses an electric arc to melt metals but generates a large heat-affected zone, leading to thermal distortion.
- Resistance Welding: Relies on electrical resistance to generate heat, often requiring high pressure and additional processing.
- Friction Welding: Uses mechanical force and heat, which may not be suitable for all materials.
Unlike these methods, laser welding ensures precise energy delivery, reducing material degradation and enhancing joint durability.
Applications of Laser Welding in High-Strength Joints
The strength and reliability of laser welding make it a preferred choice for industries where structural integrity is crucial. Some notable applications include:
- Automotive Industry: Used in chassis components, engine parts, and battery enclosures to ensure durability.
- Aerospace Sector: Essential for fabricating aircraft structures that require lightweight yet robust joints.
- Medical Devices: Ensures high-purity welds for surgical instruments and implants.
- Electronics Manufacturing: Creates precise micro-welds in delicate electronic components.
Challenges and Considerations
Despite its superior performance, laser welding requires careful parameter control. Factors such as laser power, beam focus, welding speed, and shielding gas influence the final weld quality. Operators must ensure proper setup and calibration to achieve optimal results.
Additionally, material selection plays a crucial role. Some metals, such as aluminum and copper, have high reflectivity, which can impact laser absorption. Advanced techniques like pulsed laser welding or hybrid welding help overcome such challenges.
Conclusion
Laser welding stands out as a superior welding technique due to its precision, deep penetration, refined microstructure, and controlled heat input. These factors contribute to stronger joints compared to traditional methods. By maintaining material integrity, reducing thermal stress, and eliminating excess filler materials, laser welding ensures durable and reliable welds across various industries.
What's Your Reaction?
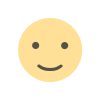
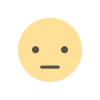
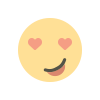

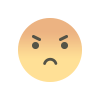
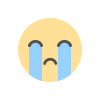
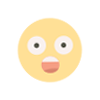