Training for Transformation: Building a Skilled Workforce for Sustainable Waste Management in Indian Biopharma
Discover how Indian biopharma companies are building a skilled workforce for sustainable waste management under Make in India and Atmanirbhar Bharat.
Training for Transformation: Building a Skilled Workforce for Sustainable Waste Management in Indian Biopharma
The Indian biopharmaceutical industry is undergoing a powerful shift toward sustainable practices. As the nation accelerates its manufacturing capacity under the Make in India initiative and envisions industrial self-reliance through Atmanirbhar Bharat, biopharma companies are increasingly expected to meet strict environmental standards—especially in how they manage industrial waste. One critical factor determining the success of these efforts isn’t just infrastructure or technology—it’s people.
Creating a sustainable waste management ecosystem within pharmaceutical manufacturing requires a skilled, informed, and environmentally conscious workforce. Engineers, facility managers, safety officers, and operational staff must be equipped with the right knowledge, tools, and mindset to handle chemical, biological, and hazardous waste responsibly. It’s no longer sufficient to rely on automated systems alone; without well-trained personnel, even the most advanced systems can fail.
A study by Pringle, Dadwal, and Kumar emphasizes that effective waste handling in Indian biopharma facilities is directly tied to workforce training. The research highlights both progress and gaps in how companies are preparing their staff for evolving environmental responsibilities. This blog explores the urgent need for capacity building, the strategies being implemented, and how human capital is shaping the future of sustainable biopharmaceutical manufacturing in India.
Why a Skilled Workforce is Central to Sustainable Waste Management
Industrial waste management, particularly in the biopharma sector, involves several complex processes:
-
Waste identification and classification
-
Segregation at source
-
Hazardous material handling
-
Documentation and labeling
-
Use of personal protective equipment (PPE)
-
Monitoring treatment systems
-
Compliance reporting
Each step carries regulatory, safety, and operational implications. Inconsistent knowledge or procedural lapses can lead to cross-contamination, non-compliance, fines, and in worst cases, environmental disasters.
Additionally, different departments—from R&D and production to maintenance and logistics—encounter various forms of waste daily. This means that waste management is not the job of a single team but a cross-functional responsibility, requiring a unified understanding across the organization.
Current Gaps in Training and Skill Development
While many leading companies have taken steps toward upskilling, several gaps still exist, especially in small and mid-sized biopharma firms.
1. Inconsistent Training Standards
There is no universal training framework or certification for waste management personnel in the pharmaceutical sector. As a result, the quality and frequency of training vary widely across companies.
2. Limited Practical Exposure
Some training programs remain theoretical, lacking hands-on sessions with treatment systems or real-world simulations.
3. Language and Accessibility Barriers
Training materials are often in English or rely on technical jargon, making them less accessible to ground-level workers who may be more comfortable in regional languages.
4. Insufficient Onboarding for New Recruits
New employees sometimes begin work before receiving full environmental safety training, leading to avoidable errors in waste handling.
As the study shows, companies that invest consistently in upskilling across all staff levels report smoother audits, fewer incidents, and better system performance.
Key Components of Effective Training Programs
To build a workforce that supports sustainable waste practices, biopharma companies are developing more comprehensive and inclusive training modules. These programs often include the following core elements:
1. Role-Specific Modules
Different job functions encounter different waste types. Engineers might work with solvents, while packaging teams handle contaminated materials. Role-based training ensures relevance and better retention.
2. SOP-Based Instruction
Training sessions aligned with Standard Operating Procedures (SOPs) make it easier for employees to apply learning on the floor. Visual SOPs and real-time demonstrations increase effectiveness.
3. Emergency Preparedness
Mock drills for spills, leaks, or equipment failure prepare teams to act decisively in critical moments. This reduces the risk of escalation and promotes a culture of safety.
4. Regulatory and Documentation Training
Staff are educated on the importance of recordkeeping, waste manifests, and audit preparedness. This ensures seamless interactions with pollution control boards and export authorities.
5. Environmental Awareness
Going beyond procedures, some companies now include basic environmental science, effects of pharmaceutical pollution, and case studies to help staff connect their work with real-world impact.
Training Delivery: Evolving Beyond Traditional Methods
To make training more engaging and impactful, companies are now experimenting with various delivery formats.
-
E-learning platforms: Accessible 24/7, these allow for self-paced learning and easy content updates.
-
Gamified modules: Points, badges, and team competitions boost participation and retention.
-
Micro-learning: Short, 5–10 minute lessons covering one topic at a time fit better into busy schedules.
-
Mobile apps: Push notifications, video tutorials, and on-the-go checklists keep training relevant.
-
Blended learning: Combining online modules with in-person workshops ensures both knowledge and skill.
These formats help reinforce learning while making it easier to track progress and performance.
Industry Collaborations and External Certifications
Recognizing the need for standardized skill development, some Indian biopharma companies are collaborating with:
-
Technical training institutes
-
Environmental NGOs
-
National Skill Development Corporation (NSDC)
-
State Pollution Control Boards
-
Industry associations like OPPI and IPA
Such collaborations support joint curriculum development, trainer certification, and third-party evaluation. In some cases, companies sponsor employees to attend certified waste handling or EHS (Environment, Health, Safety) programs.
This ensures that training remains aligned with evolving standards and introduces new technologies and best practices into the workplace.
Building a Culture of Accountability
Effective training does more than transfer knowledge—it creates a culture of responsibility. Companies that encourage employees to report unsafe practices or suggest improvements in waste handling benefit from greater transparency and innovation.
Strategies to build this culture include:
-
Recognition programs for “Sustainability Champions”
-
Inclusion of environmental KPIs in appraisals
-
Weekly team huddles to discuss observations and ideas
-
Anonymous reporting mechanisms for safety violations
When employees feel empowered and respected for their contributions, they are more likely to embrace sustainable practices voluntarily.
The Atmanirbhar Bharat Advantage
Investing in workforce development aligns directly with the goals of Atmanirbhar Bharat, which aims to build internal capabilities and reduce reliance on imported expertise or solutions. By training Indian professionals in advanced waste management techniques, the industry strengthens its resilience and competitiveness.
This also creates a ripple effect:
-
Job creation in environmental training and consulting
-
Localized innovation from technicians familiar with India’s unique industrial conditions
-
Export readiness, as global clients increasingly demand ESG disclosures and performance metrics
-
Increased MSME participation, as training levels the playing field for smaller players
Government’s Role in Scaling Impact
While industry-led efforts are growing, there is an opportunity for greater public-private collaboration. The Indian government can support this mission through:
-
National certification programs for pharma waste handlers
-
Centralized curriculum resources available in multiple languages
-
Incentives for companies that meet training milestones
-
Sector-specific modules under existing skilling missions
-
Recognition of green workforce initiatives through national awards
These steps would enhance consistency and accelerate adoption across the entire pharmaceutical ecosystem.
Looking to the Future: AI, AR, and Smart Training
As technology evolves, so will the methods of training. In the near future, Indian biopharma firms may leverage:
-
Augmented Reality (AR) simulations for interactive learning
-
AI tutors to personalize training based on learner progress
-
Predictive analytics to identify employees needing refresher sessions
-
IoT integration for real-time feedback from waste handling equipment
-
Blockchain to verify and record training completion for compliance
These tools could dramatically increase training efficiency and make knowledge sharing more dynamic and scalable.
Summary
Training is no longer an auxiliary function—it is the engine powering India’s sustainable biopharma revolution. As illustrated in the study, workforce capacity plays a decisive role in how effectively companies handle their industrial waste. A well-trained team is better equipped to minimize risks, ensure compliance, and lead environmental innovation.
By embedding training into the core of their sustainability strategies, biopharma companies are contributing meaningfully to Make in India and Atmanirbhar Bharat. They are building not only products but also people—professionals ready to create a cleaner, safer, and more responsible pharmaceutical future for India and the world.
???? Bibliography (APA Style)
Pringle, I., Dadwal, N., & Kumar, A. (2024). A questionnaire-based study on industrial waste management in Indian biopharmaceutical industries. Environment Conservation Journal, 25(4), 972–978. https://doi.org/10.36953/ECJ.28502884
What's Your Reaction?
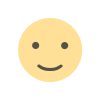
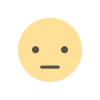
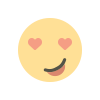

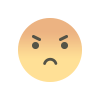
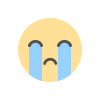
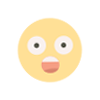