The Impact of Miniaturization on Cable Assemblies in Electronics
Explore how miniaturization is transforming cable assemblies in electronics, driving innovation, improving performance, and enabling compact, high-efficiency devices across industries.

The demand for smaller, more compact electronic devices is rapidly increasing across industries. From consumer electronics to medical devices and aerospace applications, miniaturization has become a key focus for manufacturers. As device sizes shrink,cable assemblies must evolve to maintain functionality, reliability, and performance in increasingly confined spaces.
Cable assemblies play a critical role in ensuring seamless connectivity within compact devices. The shift toward miniaturization presents significant challenges for manufacturers, but it also drives innovation in electronic cable assemblies, enabling high-performance solutions tailored for advanced applications.
Why Miniaturization is Reshaping Cable Assembly Design
Miniaturization demands more than simply reducing the size of components. It requires manufacturers to rethink designs while ensuring durability and compatibility. Electronic cable assemblies must handle high data transfer rates, power distribution, and signal integrity without compromising quality.
Space constraints and increased performance expectations are paired in sectors like aerospace, automotive, and medical technology. High-density cable designs, advanced materials, and precision manufacturing processes are essential for meeting these requirements. Miniaturized custom cable assemblies offer the flexibility to meet specific industry demands, improving device efficiency and reliability.
Key Challenges in Miniaturized Cable Assemblies
As devices become smaller, custom cable assembly manufacturers face several challenges. These include:
-
Maintaining Signal Integrity: High-density designs can increase the risk of signal interference, affecting device performance.
-
Mechanical Reliability: Reducing the size of components may compromise durability and resistance to wear.
-
Thermal Management: Compact designs often lead to increased heat generation, requiring effective heat dissipation strategies.
-
Complex Manufacturing Processes: Miniaturized assemblies demand precision engineering and specialized equipment, increasing production complexity.
Despite these challenges, ongoing advancements in materials and manufacturing technologies help manufacturers overcome these limitations, enabling the development of reliable, high-performance cable assemblies.
Innovations in Miniaturized Cable Assemblies
Recent innovations have transformed how electronic cable assemblies are designed and produced. Manufacturers are integrating advanced materials and technologies to improve durability, reduce weight, and enhance performance. Some notable innovations include:
-
Micro-Coaxial Cables: Ideal for high-frequency applications, micro-coaxial cables provide excellent signal integrity in compact designs.
-
Flat Flexible Cables (FFC): These lightweight and flexible cables are perfect for compact spaces, offering high performance in data transmission.
-
High-Density Connectors: Miniaturized connectors maximize space while maintaining reliable electrical connections.
These innovations allow manufacturers to meet the growing demand for miniaturized solutions without sacrificing performance.
Industries Benefiting from Miniaturized Cable Assemblies
Miniaturized custom cable assemblies have found applications across multiple industries, enabling advancements in technology and design.
1. Medical Devices: Compact medical devices rely on miniaturized cable assemblies for precision diagnostics and treatment solutions. High-density designs support wearable technology and minimally invasive devices.
2. Aerospace and Defense: The aerospace industry demands lightweight and durable components. Miniaturized cable assemblies improve efficiency and reduce overall weight, ensuring reliable performance in extreme environments.
3. Consumer Electronics: Devices like smartphones, laptops, and wearable technology require compact, high-performance cable solutions. Miniaturization supports thinner, more powerful devices.
4. Automotive Industry: Advanced driver-assistance systems (ADAS) and electric vehicles (EVs) rely on miniaturized cable assemblies to seamlessly integrate sensors and communication systems.
The Future of Miniaturization in Cable Assemblies
As technology continues to evolve, the trend toward miniaturization will only accelerate. The demand for compact, high-performance components will drive further innovations in electronic cable assemblies. Materials science, precision manufacturing, and advanced design tools will play a crucial role in overcoming current limitations and expanding the possibilities of miniaturized solutions.
For manufacturers, staying ahead of this trend requires a commitment to innovation and continuous improvement. Collaboration with specialized partners ensures access to cutting-edge solutions that meet industry-specific requirements.
How Star Engineering Adapts to Miniaturization
Star Engineering is at the forefront of adapting to the challenges of miniaturization. With extensive experience creating custom cable assemblies, the company provides tailored solutions for the aerospace, medical, and automotive industries. Star Engineering’s focus on quality and precision ensures that each assembly meets the highest standards of reliability and performance.
For industries requiring advanced electronic cable assemblies, Star Engineering offers innovative, customized solutions designed to meet the demands of modern technology. Contact Star Engineering Inc. to learn more about our expertise in miniaturized cable assemblies and how we can support your evolving needs.
What's Your Reaction?
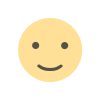
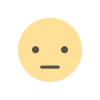
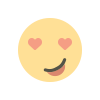

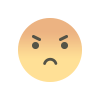
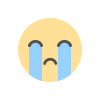
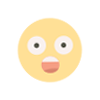