Precision CNC Machining: Revolutionizing the Manufacturing Industry

In today’s fast-paced industrial landscape, precision is the cornerstone of success. Whether it's aerospace, automotive, medical, or electronics manufacturing, the demand for high-quality, intricate parts has never been greater. One technological advancement that has dramatically transformed the manufacturing world is Precision CNC Machining.
CNC, or Computer Numerical Control, is a technology that automates the operation of machine tools like lathes, mills, and grinders. What sets precision CNC machining apart from traditional methods is its ability to produce complex, high-tolerance components with unmatched accuracy. In this article, we’ll explore what precision CNC machining is, how it works, its benefits, and its crucial role in various industries.
What is Precision CNC Machining?
At its core, precision CNC machining is a computer-controlled manufacturing process that uses pre-programmed software to control the movement of tools and machines. CNC machining can create a wide range of parts from metal, plastic, wood, or composites, all while maintaining exacting tolerances.
The term "precision" refers to the machine's ability to achieve high levels of accuracy, often within micrometers. This level of detail is critical in industries where the smallest deviation can lead to significant problems, such as in aerospace or medical device manufacturing.
How Does Precision CNC Machining Work?
The process begins with creating a 3D CAD (Computer-Aided Design) model of the part or component to be manufactured. The design is then translated into a CNC machine-readable code known as G-code. This code tells the CNC machine exactly how to move, which tools to use, and how deep to cut, based on the design specifications.
Once the machine is programmed, the material (often a solid block of metal, plastic, or composite) is secured on the machine’s bed. The CNC machine uses a variety of tools, such as drills, end mills, and lathes, to precisely cut away material, gradually shaping it into the desired component.
The key to precision lies in the CNC machine’s ability to work with extremely tight tolerances. High-end machines can repeat the same operation thousands of times with a minimal error margin, often less than 0.001 inches (or even smaller, depending on the specific machine and application).
Key Advantages of Precision CNC Machining
-
Unmatched Accuracy and Consistency: CNC machines can achieve a level of precision that’s difficult, if not impossible, to match by hand or with traditional machining methods. Whether the job involves intricate details, complex geometries, or tiny components, precision CNC machining ensures that the final product meets the exact specifications every time.
-
Complex Geometries: CNC machining allows manufacturers to produce parts with intricate shapes and complex geometries that would be time-consuming and error-prone using manual processes. Features like undercuts, internal threads, and fine surface finishes are achievable with ease.
-
Scalability and Efficiency: CNC machining isn’t just for one-off prototypes; it’s ideal for large-scale production as well. Once the machine is programmed, it can produce hundreds or even thousands of identical components, maintaining consistent quality and reducing the need for rework.
-
Versatility: Precision CNC machines can work with a wide variety of materials, including metals (like aluminum, titanium, and stainless steel), plastics, ceramics, and composites. This makes CNC machining suitable for a vast array of industries, from automotive to medical, aerospace, and beyond.
-
Cost-Effective for Large Production Runs: While the initial setup cost for CNC machining may be higher compared to traditional methods, the efficiency and speed of production over time make it a cost-effective choice, especially for larger production runs. Automated processes reduce the need for human intervention, minimizing labor costs and the potential for errors.
-
Reduced Lead Times: Precision CNC machining can significantly reduce lead times. The automation of the manufacturing process allows for faster production, and the ability to quickly change tool configurations ensures that deadlines are met without compromising quality.
Applications of Precision CNC Machining
Precision CNC machining is ubiquitous across several industries. Below are some of the key sectors where CNC machining plays a vital role:
1. Aerospace Industry:
In aerospace, precision is non-negotiable. CNC machines are used to manufacture critical components such as turbine blades, airframe parts, and engine components. These parts must meet strict tolerances to ensure safety, performance, and reliability, making CNC machining an ideal solution.
2. Automotive Manufacturing:
Automotive manufacturers rely on precision CNC machining to produce high-performance engine parts, transmission components, and custom parts. CNC machining is also integral in prototyping new designs for vehicles, allowing for faster development and testing.
3. Medical Device Manufacturing:
The medical industry often requires components with very tight tolerances, especially when it comes to surgical instruments and implants. CNC machining ensures that these products are precise, safe, and effective for use in medical procedures, reducing the risk of complications.
4. Electronics and Consumer Goods:
Precision CNC machining is widely used to produce parts for electronics, from enclosures and connectors to tiny internal components. These components require not only high accuracy but also the ability to work with materials like circuit board substrates and heat-resistant plastics.
5. Defense and Military:
CNC machining plays a key role in the production of defense-related components, such as weapon systems, armor-piercing projectiles, and communication systems. Parts in this sector must meet extremely high standards of durability, performance, and accuracy.
6. Energy and Oil & Gas:
In the energy sector, CNC machining is used to create critical parts for drilling equipment, power generation systems, and turbine components. The ability to manufacture parts with high precision ensures the reliability and efficiency of energy systems.
Emerging Trends in Precision CNC Machining
As technology continues to advance, so too does CNC machining. Some of the key trends shaping the future of precision machining include:
-
Integration with 3D Printing: The rise of additive manufacturing (3D printing) is complementing CNC machining. Manufacturers are beginning to combine the benefits of both technologies, using 3D printing for rapid prototyping and CNC machining for finishing high-precision parts.
-
Automation and AI: Artificial intelligence and machine learning are making their way into CNC machining. Smart machines equipped with AI can monitor performance, detect anomalies, and even make adjustments autonomously, further increasing efficiency and reducing the chance of defects.
-
Improved Materials: As industries demand more from their components, CNC machining is evolving to handle new and advanced materials. From high-performance alloys to bio-compatible materials for medical use, the scope of materials is expanding.
-
Increased Customization: With advancements in software and machine capabilities, CNC machining can handle more complex, customized parts. This is particularly useful in industries like aerospace and medical devices, where tailor-made components are essential.
Conclusion
Precision CNC machining is a game-changer in the world of manufacturing. Its ability to produce parts with extreme accuracy, speed, and consistency has made it indispensable across multiple industries. As technology evolves, CNC machining continues to push the boundaries of what’s possible, enabling manufacturers to create parts that are stronger, lighter, and more reliable than ever before.
For businesses looking to stay ahead of the curve, embracing precision CNC machining is not just a necessity—it's a competitive advantage. Whether you’re producing a prototype or scaling up for mass production, CNC machining will undoubtedly remain a driving force in the manufacturing sector for years to come.
What's Your Reaction?
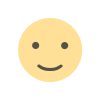
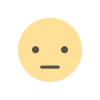
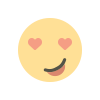

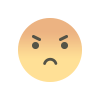
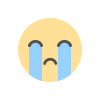
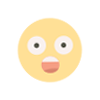