Cutting-Edge Precision: How Custom Wire EDM Machining Revolutionizes Complex Part Manufacturing

In the world of precision manufacturing, few technologies offer the accuracy and versatility of Custom Wire EDM (Electrical Discharge Machining) services. This advanced machining process uses a thin, electrically charged wire to cut intricate shapes from hard metals with micron-level precision. Unlike traditional cutting methods, Wire EDM doesn’t rely on physical force, making it ideal for delicate, complex, or ultra-hard materials that would be difficult or impossible to machine otherwise. Industries such as aerospace, medical device manufacturing, automotive, and tool & die making rely on Wire EDM for its ability to produce burr-free, stress-free cuts with exceptional accuracy.
Why Custom Wire EDM Machining Stands Out
Custom Wire EDM Machining is a game-changer for manufacturers who need high precision, intricate geometries, and superior surface finishes. Because it uses electrical sparks to erode material rather than mechanical cutting, it can handle even the toughest metals without introducing heat distortion or mechanical stress. Below, we explore the key benefits, applications, materials, and selection criteria for Wire EDM services.
1. Unmatched Precision for Complex Geometries
Wire EDM excels at producing tight tolerances (±0.0001 inches) and intricate designs, including:
-
Micro-sized holes and slots
-
Sharp inside corners
-
Thin walls and delicate features
-
Tapered cuts (using CNC-controlled wire guidance)
This makes it indispensable for injection molds, gears, and aerospace components where exact dimensions are critical.
2. No Heat-Affected Zones or Mechanical Stress
Since Wire EDM is a non-contact, thermal erosion process, it doesn’t generate the mechanical forces or heat that can warp or weaken machined parts. This is crucial for:
-
Medical implants (surgical tools, bone screws)
-
Aerospace components (turbine blades, fuel system parts)
-
Tool & die applications (punches, molds, extrusion dies)
3. Ability to Cut Hardened Metals with Ease
Traditional machining struggles with hardened steels, tungsten, and exotic alloys, but Wire EDM cuts them effortlessly. Common materials include:
-
Tool Steels (D2, H13)
-
Titanium & Inconel
-
Carbide & Tungsten
-
Beryllium Copper
4. Smooth Surface Finishes Without Secondary Processing
Wire EDM produces fine surface finishes (as low as Ra 8 µin), reducing or eliminating the need for additional polishing or grinding. This saves time and cost in post-processing, especially for:
-
Optical components
-
High-precision seals
-
Fine blanking dies
Industries That Benefit from Custom Wire EDM Machining
From medical devices to high-performance automotive parts, Wire EDM is critical in:
-
Medical & Dental – Surgical instruments, implantable devices
-
Aerospace & Defense – Turbine blades, fuel nozzles, missile components
-
Automotive – Transmission parts, fuel injectors
-
Electronics – Micro connectors, semiconductor components
Choosing the Right Wire EDM Service Provider
When selecting a Wire EDM machining partner, consider:
✔ Machine Capabilities (Multi-axis EDM, hole-drilling EDM)
✔ Material Expertise (Experience with your specific alloy)
✔ Tolerances & Finishes (Ability to meet your precision requirements)
✔ Quality Certifications (ISO 13485 for medical, AS9100 for aerospace)
Conclusion
Custom Wire EDM machining is the ultimate solution for precision cutting of complex, hardened, or delicate metal parts. Whether you need intricate molds, aerospace components, or medical devices, partnering with an experienced Wire EDM service ensures flawless results with tight tolerances and superior finishes.
What's Your Reaction?
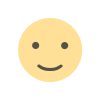
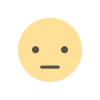
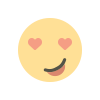

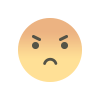
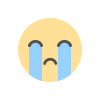
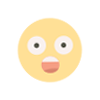