Comprehensive Guide to Industrial Strainers: Types, Applications, and Best Practices

In industrial processes, maintaining the purity of fluids and gases is paramount to ensure the longevity and efficiency of equipment. Strainers serve as vital components in achieving this by filtering out unwanted particles and debris. This guide delves into the various types of industrial strainers, their applications, and best practices for optimal performance.
Understanding Industrial Strainers
Industrial strainers are devices installed in pipelines to remove suspended solids from liquids or gases. By capturing debris, they prevent contamination, reduce maintenance costs, and protect downstream equipment from potential damage.
Types of Industrial Strainers
1. Y-Type Strainers
Design and Functionality
Y Type strainers, named for their Y-shaped configuration, are versatile devices used to filter out foreign particles from pipelines. They are suitable for both liquid and gas applications and can be installed in horizontal or vertical pipelines. Their compact design makes them ideal for systems with space constraints.
Applications
-
Steam Systems: Protecting control valves and traps from debris.
-
Liquid Applications: Filtering water, oil, and chemicals in various industries.
-
Gas Applications: Ensuring purity in gas lines by removing particulate matter.
Advantages
-
Compact and versatile installation.
-
Suitable for high-pressure applications.
-
Easy maintenance with a blow-off valve for cleaning without disassembly.
2. Basket Strainers
Design and Functionality
Basket strainers feature a cylindrical or basket-shaped screen that captures debris from the flow. They are primarily used in liquid applications and offer a larger straining area compared to Y-Type strainers, which results in a lower pressure drop.
Applications
-
Water Treatment: Removing debris from cooling water and process water systems.
-
Petrochemical Industry: Filtering hydrocarbons to protect sensitive equipment.
-
Food and Beverage: Ensuring product purity by removing contaminants from liquids.
Advantages
-
High dirt-holding capacity due to the large straining area.
-
Suitable for applications requiring fine filtration.
-
Easy removal and cleaning of the straining element.
3. T-Type Strainers
Design and Functionality
T Type strainers, also known as T-strainers, have a T-shaped design and are used for coarse filtration. They are typically custom-built and are installed in horizontal pipelines. These strainers are suitable for applications where temporary or permanent filtration is needed.
Applications
-
Chemical Processing: Protecting pumps and heat exchangers from debris.
-
Oil and Gas: Filtering out contaminants in pipelines to prevent equipment damage.
-
Power Generation: Ensuring clean water supply to boilers and turbines.
Advantages
-
Customizable design to meet specific application requirements.
-
Robust construction suitable for high-pressure environments.
-
Can be designed for both temporary and permanent installations.
4. Duplex Basket Strainers
Design and Functionality
Duplex basket strainers consist of two basket strainer chambers and a diverting valve, allowing continuous operation during maintenance. When one basket requires cleaning, the flow can be diverted to the other, ensuring uninterrupted filtration.
Applications
-
Continuous Process Industries: Such as paper mills and chemical plants where shutdowns are costly.
-
Marine Applications: Filtering seawater in cooling systems without interrupting operations.
-
Pharmaceuticals: Maintaining sterile conditions by ensuring continuous filtration.
Advantages
-
Enables continuous operation without shutdowns.
-
Easy switching between strainer baskets for maintenance.
-
Reduces downtime and maintenance costs.
5. Temporary and Conical Strainers
Design and Functionality
Temporary strainers, including conical (cone-shaped) and truncated designs, are used during the startup of pipelines to remove debris resulting from construction and commissioning. They are installed temporarily and removed after the initial cleaning process.
Applications
-
Pipeline Commissioning: Capturing welding slag, rust, and other debris during startup.
-
Hydrostatic Testing: Ensuring debris-free pipelines before operational use.
-
Short-Term Filtration Needs: Situations where permanent filtration isn't necessary.
Advantages
-
Cost-effective solution for temporary filtration needs.
-
Easy installation and removal.
-
Protects equipment during initial operations.
Best Practices for Strainer Selection and Maintenance
-
Material Compatibility: Ensure the strainer material is compatible with the fluid or gas to prevent corrosion and contamination.
-
Regular Maintenance: Implement a routine cleaning schedule to prevent clogging and ensure optimal performance.
-
Pressure Drop Monitoring: Regularly monitor pressure drop across the strainer to detect blockages early.
-
Proper Sizing: Select a strainer size that accommodates the flow rate and desired level of filtration without causing excessive pressure loss.
Conclusion
Selecting the appropriate strainer type is crucial for maintaining the efficiency and longevity of industrial systems. By understanding the distinct features and applications of each strainer, industries can make informed decisions, ensuring optimal performance and protection of their equipment.
What's Your Reaction?
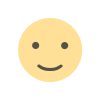
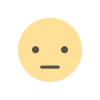
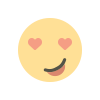

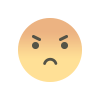
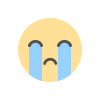
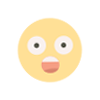