An AAC conductor is made entirely of aluminum, why doesn’t it melt under high electrical loads
AAC (All Aluminum Conductor) is widely used in power transmission and distribution, primarily in urban areas and for short-distance applications
AAC (All Aluminum Conductor) is widely used in power transmission and distribution, primarily in urban areas and for short-distance applications. Since it is made entirely of aluminum, one might wonder why it doesn’t melt when carrying high electrical loads. To answer this, we need to explore multiple aspects, including the electrical and thermal properties of aluminum, the behavior of conductors under load, heat dissipation mechanisms, and real-world applications.
1. Understanding the Melting Point of Aluminum
Before diving into the specifics of AAC conductor, let’s first understand the melting properties of aluminum:
- Melting Point of Aluminum: 660.3°C (1220.5°F)
- Boiling Point of Aluminum: 2470°C (4478°F)
This means that for an AAC conductor to melt, its temperature must exceed 660.3°C. In practical applications, the temperature of a conductor rarely reaches such extreme levels due to various controlling factors.
2. Electrical Resistance and Heat Generation
When an electrical current passes through an AAC conductor, it encounters some resistance, which leads to heat generation. The relationship between current, resistance, and heat follows Joule’s Law, which states:
Where:
- P = Power dissipated as heat (Watts)
- I = Current (Amperes)
- R = Resistance (Ohms)
Although aluminum has a higher electrical resistance compared to copper, AAC conductors are designed with a larger cross-sectional area to compensate for this resistance. By increasing the diameter, the overall resistance is reduced, which in turn lowers heat generation.
3. Heat Dissipation Mechanisms in AAC Conductors
Heat dissipation plays a crucial role in preventing the conductor from reaching its melting point. The primary mechanisms through which AAC conductors dissipate heat are:
3.1 Convection
The surrounding air helps cool the conductor. The movement of air (natural convection) carries away heat, preventing excessive temperature rise.
3.2 Radiation
The conductor emits heat in the form of infrared radiation. This process helps in maintaining a balanced temperature under normal operating conditions.
3.3 Conduction
The heat generated within the conductor is also transferred along its length, reducing the chances of localized heating.
4. Influence of Load Current on Temperature Rise
The operating temperature of an AAC conductor is influenced by the current it carries. Utilities set limits on the amount of current to ensure that the conductor remains within a safe operating temperature range.
Typical operating temperatures for AAC conductors are:
- Normal Operation: 75°C – 90°C
- Emergency Loading: Up to 110°C
- Short Circuit Condition: Can reach up to 250°C momentarily, but this is within safety limits
As long as the current remains within rated values, the conductor temperature stays well below the melting point of aluminum.
5. External Factors Affecting Conductor Temperature
Several external factors influence the temperature of AAC conductors and their ability to withstand high electrical loads without melting:
5.1 Ambient Temperature
Higher ambient temperatures can cause an increase in conductor temperature, but well-designed systems consider this factor in load calculations.
5.2 Wind Speed and Direction
Increased wind speed enhances cooling through convection, lowering the conductor’s operating temperature.
5.3 Solar Radiation
Sunlight can add to the heat load of an overhead conductor, but it is typically accounted for in conductor ratings.
5.4 Altitude
At higher altitudes, the air density is lower, reducing the effectiveness of convective cooling. However, conductors are rated based on environmental conditions.
6. Special Coatings and Surface Treatments
To enhance the performance of AAC conductors and minimize excessive heating, manufacturers sometimes apply special coatings or surface treatments. These treatments can:
- Improve emissivity to enhance heat radiation
- Reduce surface oxidation, which can increase resistance
- Provide better performance in harsh environmental conditions
7. Real-World Engineering Considerations
Engineers ensure that AAC conductors do not reach their melting point by:
- Proper Sizing – Selecting the appropriate conductor size based on the expected electrical load.
- Thermal Analysis – Studying the heat dissipation characteristics under various load conditions.
- Load Balancing – Distributing electrical loads efficiently across multiple conductors.
- Monitoring Systems – Using temperature sensors and real-time monitoring to prevent overheating.
8. Comparison with Other Conductors
To better understand why AAC doesn’t melt under high loads, let’s compare it with other commonly used conductors:
Conductor Type | Composition | Electrical Conductivity | Resistance | Operating Temperature |
---|---|---|---|---|
AAC (All Aluminum Conductor) | 100% Aluminum | Moderate | Higher than Copper | 75-90°C |
ACSR (Aluminum Conductor Steel Reinforced) | Aluminum + Steel Core | Moderate | Lower than AAC | 75-90°C |
AAAC (All Aluminum Alloy Conductor) | Aluminum Alloy | Higher than AAC | Lower than AAC | 90-110°C |
Copper Conductor | 100% Copper | High | Lowest | 90-110°C |
AAC is specifically designed for short-distance, low-to-medium voltage applications where temperature rise can be managed effectively.
9. Safety Measures to Prevent Melting
To prevent overheating and potential melting, engineers implement safety measures such as:
- Load Management: Ensuring that the conductor is not overloaded.
- Use of Insulated Spacers: Preventing short circuits and excessive current flow.
- Regular Inspections: Identifying and addressing any damage or degradation.
- Protective Relays: Automatically disconnecting power in case of faults.
10. Conclusion: Why AAC Doesn’t Melt Under Load
To summarize, an AAC conductor doesn’t melt under high electrical loads because:
- Its melting point (660.3°C) is significantly higher than its maximum operating temperature (75-90°C).
- It is designed with an appropriate cross-section to limit resistance and heat generation.
- It efficiently dissipates heat through convection, radiation, and conduction.
- External factors like wind and ambient temperature help regulate its temperature.
- Real-world engineering practices ensure that the conductor operates within safe limits.
Thus, as long as AAC conductors are properly designed and installed, they remain a reliable and safe choice for electrical power transmission and distribution without the risk of melting under standard operating conditions.
What's Your Reaction?
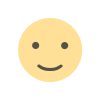
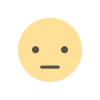
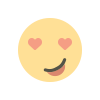

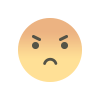
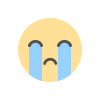
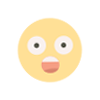