Advanced Leak Detection for Maximum Welding Efficiency
Enhance welding efficiency with advanced leak detection, ensuring precision, safety, and reduced downtime for optimal performance and cost savings.
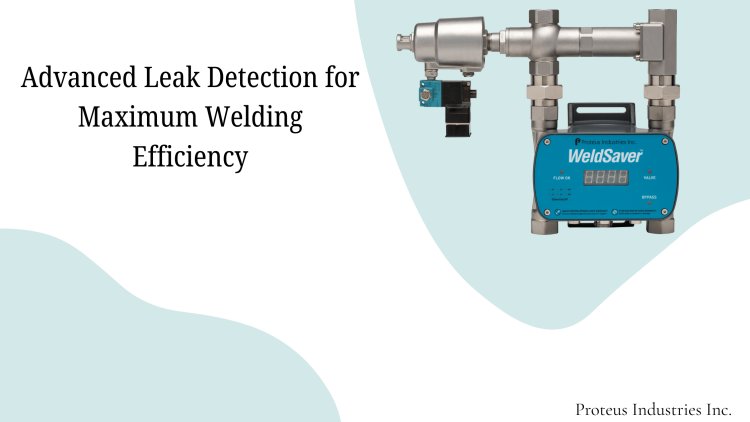
Welding is a critical process in various industries, from automotive to aerospace, where precision and efficiency are essential. However, undetected leaks in coolant and gas systems can compromise weld quality, lead to equipment failure, and increase operational costs. This is where accurate leak detection plays a vital role in maintaining maximum welding efficiency.
Advanced leak detection systems help identify even the smallest leaks in real-time, ensuring optimal performance and preventing costly downtime. By incorporating modern technologies such as automated sensors and real-time monitoring, manufacturers can significantly reduce defects and enhance safety. Accurate leak detection ensures that welding processes remain consistent, improving overall productivity and quality.
For industries that rely on high-precision welding, investing in advanced leak detection technology is a game-changer. It not only extends the lifespan of equipment but also enhances operational efficiency, making it an essential tool for businesses focused on high-quality production.
The Importance of Leak Detection in Welding
Leak detection in welding is critical for maintaining optimal efficiency, quality, and safety. A welding setup often relies on gas shielding, cooling water circulation, and controlled atmospheres to produce precise welds. Even the smallest leak in these systems can lead to compromised weld integrity, increased defects, and material wastage. The failure to detect and rectify leaks can result in costly repairs, rework, and even safety hazards for workers. With the growing demand for high-precision welding, industries are adopting advanced methods of leak detection to enhance performance and reliability.
Leaks in welding processes typically stem from various sources, such as cracks in hoses, loose fittings, and deteriorated seals. Traditional leak detection methods, such as visual inspections and soap bubble tests, often fail to identify micro-leaks that can significantly impact welding efficiency. This is where modern, technology-driven leak detection systems come into play, offering superior accuracy and reliability.
How Accurate Leak Detection Works
Accurate leak detection involves using advanced technology to identify leaks in real time, ensuring the welding process remains uninterrupted and efficient. One of the most effective systems for leak detection in welding is the WeldSaver technology developed by Proteus Industries. This system is specifically designed to detect leaks in cooling water circuits, a crucial aspect of ensuring the longevity and performance of welding equipment.
Modern leak detection solutions use various techniques, including ultrasonic sensors, pressure decay methods, and flow monitoring. These technologies allow manufacturers to pinpoint even the smallest leaks, preventing significant losses in productivity. Ultrasonic sensors detect sound waves generated by escaping gases or fluids, making them highly effective for identifying leaks that are not visible to the naked eye. Pressure decay methods involve monitoring pressure drops within a sealed system to identify potential leaks. Flow monitoring systems continuously track the rate of fluid or gas movement, instantly flagging any irregularities that indicate a leak.
By implementing advanced leak detection systems, manufacturers can improve welding efficiency by minimizing downtime, reducing waste, and enhancing the overall quality of welded components. Furthermore, accurate leak detection ensures compliance with industry regulations, helping businesses avoid penalties and liabilities associated with defective welding operations.
Enhancing Welding Efficiency with Leak Detection Technology
A well-optimized welding process is one that minimizes disruptions and maximizes output. Leak detection technology plays a significant role in ensuring seamless operations by preventing equipment malfunctions and inefficiencies. In water-cooled welding systems, detecting leaks in the cooling circuit is essential for preventing overheating and maintaining consistent weld quality. The WeldSaver system, for instance, continuously monitors coolant flow and provides immediate alerts when a leak is detected, allowing operators to take corrective action before a minor issue escalates into a major problem.
Accurate leak detection not only enhances efficiency but also improves workplace safety. Gas leaks, particularly in welding environments, can pose serious health risks to workers and increase the likelihood of fire hazards. By incorporating automated leak detection systems, industries can create a safer work environment while ensuring compliance with occupational safety standards. Additionally, reducing leaks translates to lower energy consumption and operational costs, making leak detection a cost-effective solution for welding businesses.
The integration of leak detection technology into welding operations also supports predictive maintenance strategies. Rather than waiting for equipment failure to occur, manufacturers can proactively monitor system performance and address potential issues before they lead to costly downtimes. This proactive approach extends the lifespan of welding equipment and enhances overall productivity.
Choosing the Right Leak Detection System for Welding
Selecting the most suitable leak detection system depends on several factors, including the type of welding process, the materials used, and the specific challenges faced in the production environment. High-precision industries, such as aerospace and medical device manufacturing, require highly sensitive leak detection systems to maintain strict quality standards.
Proteus Industries' WeldSaver system is a prime example of an advanced leak detection solution designed for welding applications. With its ability to monitor flow rates, detect leaks instantly, and prevent overheating, WeldSaver has become an industry standard for ensuring reliable welding operations. Other advanced leak detection technologies include helium leak detectors, thermal imaging cameras, and laser-based sensors, each offering unique advantages depending on the application.
Businesses looking to implement leak detection solutions should consider factors such as sensitivity, real-time monitoring capabilities, ease of integration, and maintenance requirements. Investing in a high-quality leak detection system ultimately leads to improved welding efficiency, reduced defects, and enhanced overall production outcomes.
The Future of Leak Detection in Welding
As technology continues to evolve, leak detection systems are becoming more sophisticated and efficient. The integration of artificial intelligence into leak detection technology is set to revolutionize the welding industry. powered systems can analyze vast amounts of data in real-time, identifying patterns and predicting potential leaks before they occur. IoT-enabled sensors allow for remote monitoring and automated alerts, further enhancing the accuracy and responsiveness of leak detection processes.
Advancements in sensor technology and data analytics are also making leak detection systems more cost-effective and accessible to businesses of all sizes. With the rise of Industry 4.0, manufacturers are increasingly adopting smart solutions to optimize their welding operations and achieve higher levels of efficiency. The future of welding will see greater integration of automated leak detection systems, reducing the need for manual inspections and minimizing the risk of production disruptions.
Conclusion
Accurate leak detection is a critical component of achieving maximum welding efficiency. By utilizing advanced technologies such as ultrasonic sensors, pressure monitoring, and AI-driven detection systems, manufacturers can significantly reduce downtime, enhance product quality, and improve workplace safety. The adoption of innovative leak detection solutions, such as Proteus Industries' WeldSaver, ensures that welding processes remain efficient, cost-effective, and compliant with industry standards.
As welding technology continues to advance, businesses must stay ahead by integrating the latest leak detection systems into their operations. Investing in accurate leak detection not only prevents costly defects but also enhances overall productivity and sustainability. In an industry where precision and reliability are paramount, implementing cutting-edge leak detection technology is the key to achieving long-term success.
What's Your Reaction?
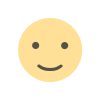
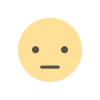
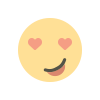

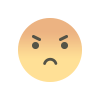
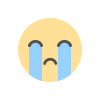
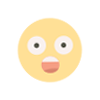